Bringing benefits to the bottom line and assembly line
EnerSys® manufactures an array of high-quality batteries and other energy storage products. During the manufacturing process, there are multiple steps that require the use of hands-on power tools to assemble and finalize these products to ensure they are ready to be shipped to customers. These tools all need a power source. A popular and traditional power source is compressed air – a system in which a large centrally-powered compressor maintains constant pressure in a chamber which then powers the hand tools through the conversion of potential energy into kinetic energy. However, compressed air systems are often far larger than the circumstances for which they are used and, over time, are prone to leaks that can be inefficient and energy intensive. Additionally, due to the one-size-fits all nature of these compressed air tools, they can cause variabilities or inconsistencies in assembly. As a battery manufacturer that focuses on quality and efficiency, we knew we needed to scope out a better way.
Chris Craig, VP of Global Systems & Lithium Operations, decided to take this matter into his own hands. Following some thorough market research, Chris, along with Dwayne Gray, Spokane Plant Manager, and Dan Woods, Senior Manufacturing Engineer Manager, determined that switching to lithium-ion battery powered smart tools would solve this problem. This solution would bring multiple benefits to both the assembly line and our bottom line. Our Spokane, Washington site was first to make this switch, and the other assembly sites – Suwanee, Georgia; Bellingham, Washington; and Burnaby, Canada – soon followed.
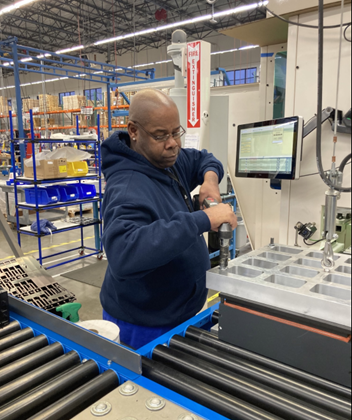
These electric and cordless smart tools maintained quality and improved efficiency, reducing the number of products that failed to meet our high standards – which also meant reducing waste. “Since they are smart tools, they can be calibrated to use just the right amount of force, torque, and rotations to ensure extremely consistent quality throughout the variety of products we manufacture,” says Chris Craig. The changes are also leading to a reduction in material waste and offer overall reduced energy consumption because they no longer rely on an “always on” compressed air system. This means that not only are we reducing our environmental footprint, but we are also showing a positive return on investment – and, far more quickly than originally anticipated.
“Historically, we’ve had to replace our air compression tools every 2-3 years,” says Chris. “With the new industrial-grade electric smart tools, they’re expect to last over 5 years. Investing in better tools and machinery that deliver better results is one way we’re working to improve efficiencies, make progress on our sustainability goals and save money at the same time.”
EnerSys employees utilizing lithium-ion battery-powered smart tools.